EBRI: Low carbon, big impact: Making the most of biowaste
Making useful materials from biological waste streams using pyrolysis
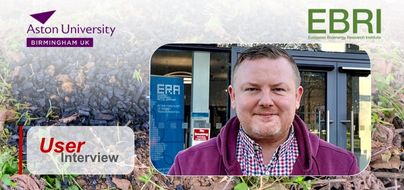
Energy And Bioproducts Research Institute
-
INDUSTRY
Environment, Clean Energy, Carbon neutrality
-
KEYWORD
Biowaste, Energy, Pyrolysis
-
INTRODUCTION SERVICE&PRODUCTS
Nexis GC-2030
Pyrolysis of bio-derived waste has the potential to provide a lower-carbon, more sustainable way of producing chemicals that are currently made from petrochemicals. But with biowaste feedstocks being so diverse, how can we determine the best use of a particular resource? We talk to Dr Daniel Nowakowski at Aston University’s Energy and Bioproducts Research Institute (EBRI) about the challenges faced when thermally processing biowaste, and how collaborating with Shimadzu is helping him and his team to maximise the potential benefits of these feedstocks.
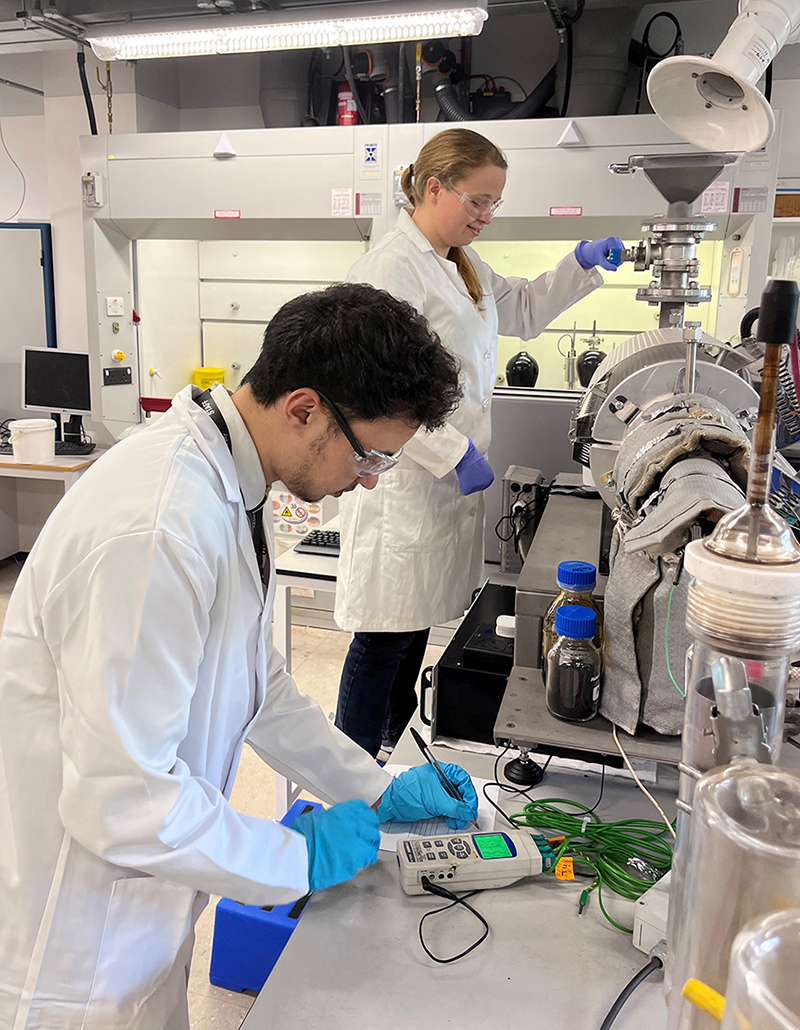
Adam Elaradi and Dr Sarah Asplin operate the laboratory-scale intermediate pyrolysis system
As Lecturer in Chemical Engineering and Applied Chemistry at EBRI, Dr Nowakowski has first-hand knowledge about the types of biowaste sources and the ways in which the resulting products can be used – from carbon-storing soil conditioners to sustainable fuels. When the team is given a biowaste sample to investigate, he says, we ask one question: “How can we tailor the pyrolysis process to derive products with the greatest value or benefit?”.
Also, he adds, nothing goes to waste: “Unlike in conventional charcoal production, we’re not just interested in the solid matter left behind – we also capture all the vapours and gases emitted, in order to extract value from them too”, he explains.
One of the first steps when understanding the potential of a new material, is to carry out a thermal degradation (TD) study. At the same time, the gases released can also be sent straight to a detector, again to provide a first impression of what the sample contains. More information on the products obtained from TD is then obtained by micropyrolysis–GC–MS. This uses what is in essence a miniature version of the full-scale pyrolysis equipment, with a gas chromatograph–mass spectrometer fitted to the outlet, configured to analyse the vapour-phase products.
The advantage of this setup, says Dr Nowakowski, is its speed – “in just an hour, you can complete the preparation and analysis of a test sample, and get an idea of the vapours that could be obtained from the feedstock”, he explains.
Bioliquids as fuel additives and antifungal agents
One of the applications of bioliquids that Dr Nowakowski and colleagues are working on is so-called ‘wood vinegar’. Dr Nowakowski explains: “These liquids have received a lot of hype as ‘natural’ antifungals and antibacterials, but there’s little information about exactly what they contain, let alone studies into their environmental and health impacts”. This research is vital, he adds. “Wood vinegar definitely has potential for treating mould and bacterial films, but there’s a big issue around process and quality control. For example, if the pyrolysis temperatures are too high, the product can contain toxic aromatics, dioxins, and chlorine-containing chemicals. If you’re applying the wood vinegar to crops, they’ll end up in the environment, which is something you certainly don’t want”.
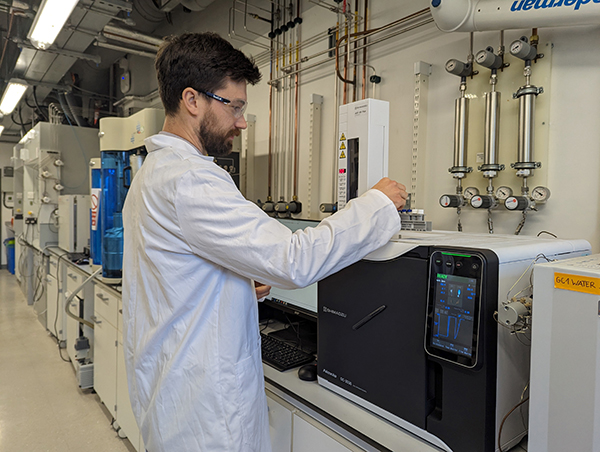
Dr Christopher Thomas working with
‘simulated distillation’ system, consisting of a Shimadzu Nexis GC-2030 with SimDist software
This is just a flavour of the work that’s going on at EBRI, says Dr Nowakowski. Through all of his work as a researcher and laboratory manager at EBRI, Shimadzu has been there for him, explains Dr Nowakowski. “Right from 2013 when we were setting up the new laboratories for bioenergy research here at EBRI, I’ve been able to benefit from their expertise in analytical chemistry”, he says.
This collaboration has continued to the present day, he adds, with guidance on getting the most out of the equipment, as well as routine maintenance and timely support. “With so many people booking our equipment, business continuity is very important for us – so it’s great that we always have a quick response from Shimadzu!”, he says. “There’s so much going on – and it’s good to know that Shimadzu will be there for us, ready to help with anything I need!”, he concludes.
Dr Daniel Nowakowski
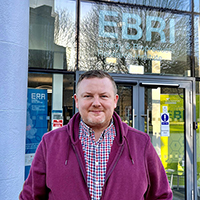
Dr Daniel Nowakowski is a Lecturer in Chemical Engineering and Applied Chemistry at Aston University (Birmingham, UK), and Laboratory Manager of Aston’s Energy and Bioproducts Research Institute (EBRI). Following undergraduate studies in Chemical Technology in Gliwice (Poland), he completed his Ph.D. degree in Environmental Catalysis at the University of Leeds (UK) in 2007. The same year, he joined Aston University as a post-doctoral research assistant, and since 2012 he has held several senior fellowship posts. He has been an active researcher since 2007, and has been involved in a wide variety of research projects and collaborations relating to the processing, analysis and application of biomass and pyrolysis products.
*Affiliates and titles of the interviewee are current as of the time of reporting.
Energy And Bioproducts Research Institute (EBRI), Aston University