Pressure Fluctuations
HPLC Troubleshooting Course
1 - Basics of Systematic Troubleshooting
2 - Preventive Maintenance Measures
4 - Pressure Fluctuations
5 - Changes in Peak Shape - Part 1
6 - Changes in Peak Shape - Part 2
5 - Ghost Peaks
8 - Peak Area Fluctuations
9 - Retention Time Fluctuations - Part 1
10 - Retention Time Fluctuations - Part 2
11 - Column Lifespan - Part 1
12 - Column Lifespan - Part 2
13 - Detector Issues
14 - Flow Line Leakage
15 - Course Summary
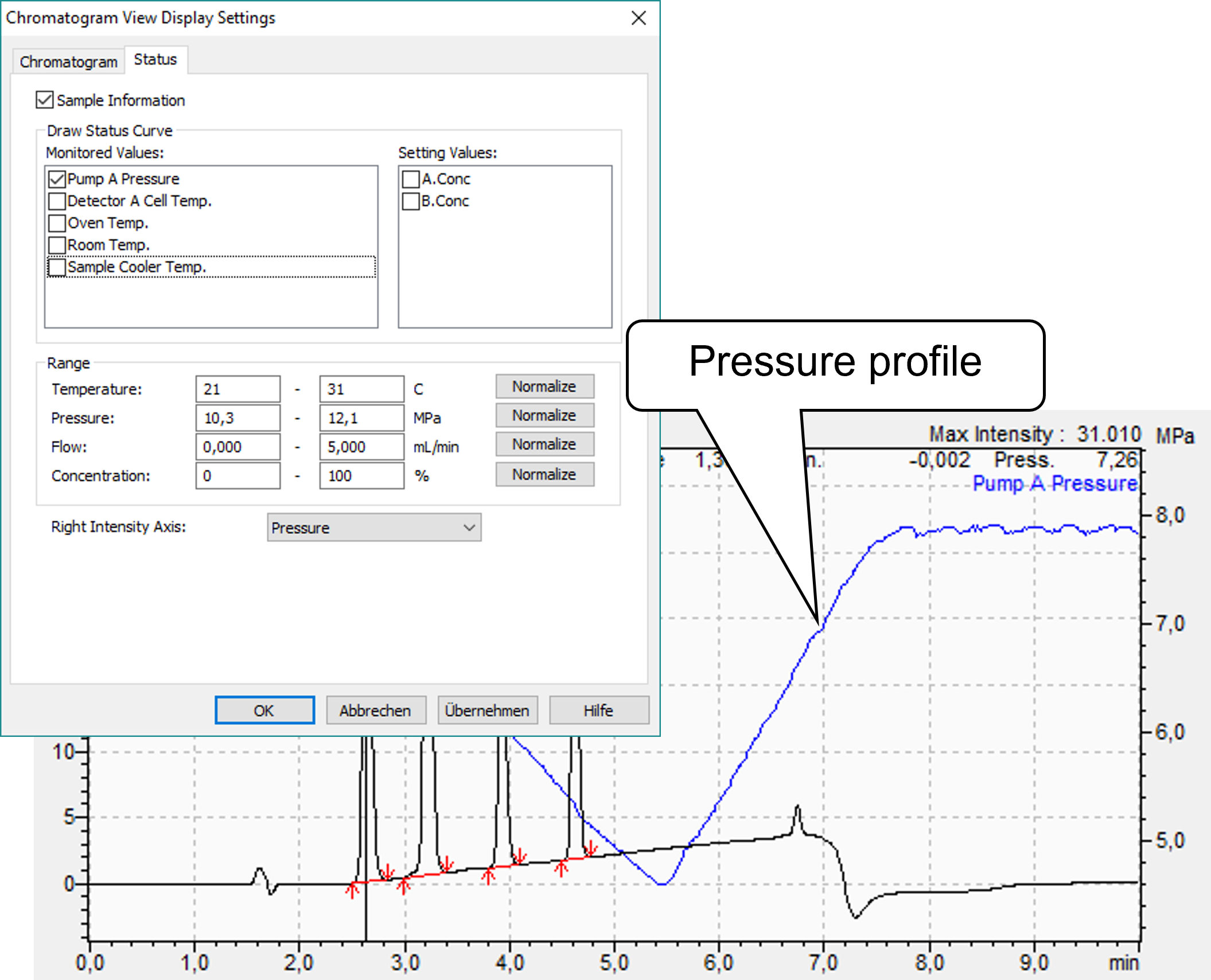
The back pressure of LC instruments is similar to a heartbeat; if it is out of sync, it becomes very noticeable in the chromatograms. As such, the pressure trace is possibly the most useful tool for understanding and resolving errors. Therefore, it is recommended to always have the pressure trace displayed and take a quick look at the pressure profile while running methods.
Every LC instrument manufacturer will be able to show the pressure trace on the chromatogram. In LabSolutions, you can display the pressure via a right-click in the chromatogram under the point "Display Setting" – "Status". Even if it is not displayed, the pressure is always recorded with every data file and can be displayed during the evaluation.
The causes of pressure fluctuation are varied. They can either be caused by the hardware, by contamination of the eluents, particles in the samples, crystallised buffer, or similar contaminants that clog the system. Even small contaminants can lead to a slow but steady increase in back pressure. As mentioned in an earlier module, temperature also plays a major role. If the temperature rises, the viscosity of the eluent decreases and consequently the pressure also decreases.
However, there are also pressure fluctuations that are completely normal and do not cause concern. For example, if a method using a gradient is run, we actively mix two or more liquids of different densities and viscosities. The result is a uniform increase or decrease in pressure which, in most cases, corresponds to the change in the mobile phase gradient.
1. Pressure fluctuations

Pressure fluctuations can appear for many different reasons. For example, if the pressure profile has a sawtooth pattern, the check valves (inlet and outlet valves of the pump heads) are usually the cause. This can occur when using high proportions of acetonitrile, as the stabilisers and any polymerised acetonitrile can deposit in the check valve. If this is the case, try flushing the check valves can be flushed with a syringe and hot water. Alternatively, the check valves can be removed and cleaned in an ultrasonic bath. If neither of these points were successful, consider replacing the check valves.
If the typical back pressure of the system has dropped and the pressure profile has irregular fluctuations, air bubbles in the solvent lines are often the cause. In this case, the lines to the reservoirs should be purged. Air bubbles in your autosampler can also cause pressure fluctuations. If you suspect this to be the case, purge the rinse solutions and flush your autosampler. If there are no more air bubbles in the system, but the pressure fluctuations persist, the piston seals may need replacing. Finally, any leaks in the system can also cause pressure fluctuations. Try each approach one at a time until you find the cause of the issue:

1. Check if there are air bubbles in the system and remove them
2. Check the status of the pump and piston seals. If the pressure profile has a sawtooth pattern, clean or replace the check valves
3. Check the system for leaks
2. Too high pressures

If the back pressure is higher than normal, the column, column guard, a clogged inline filter or a blockage is usually the cause. The best way to find the cause is to follow the solvent flow path from the reservoirs, loosening the first connection at the pump. You can loosen the first connection at the pump and successively work your way along the flow path. If the pressure rises sharply, the source of the blockage is identified. If it is within part of the tubing, you can remove it and try to flush it free directly at the pump in the opposite direction. This way, you do not flush the contamination through your system. If it is the column, some columns can be back-flushed but often a replacement column is needed. Please contact the manufacturer of your column to see what the options are. If you often have problems with clogged columns, it is advisable to use a guard column. These can be replaced more easily and are cheaper than your analytical column.
3. Too low pressures
If the back pressure is lower than normal, it can be caused by a leak or an air bubble in the pumps. If the air bubble is very stubborn and cannot be removed by purging, you can help by attaching a syringe at the waste outlet of the purge valve and pulling a slight vacuum. The use of solvents with low surface tension, such as methanol, can also dissolve stubborn air bubbles.
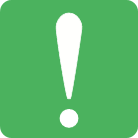
Things to consider daily:
Eluents:
- Filter when using high salt concentrations
- If the instrument is not used, flush the system through with clean solvent - no buffer should remain in the LC system
- Use eluents well within their limited shelf-life
- Pay attention to the purity of the solvents and especially ensure that the water purification systems are regularly maintained
Samples:
- Filtering samples is very important - particulates from unfiltered samples can clog instrument flow paths and columns
- Centrifuging samples can help to remove large molecules and particulates
- If necessary, also perform additional purification steps, such as protein precipitation
- Verify compatibility with the eluents
- Flush the injector if samples with high salt content were used
- Try to keep the ambient temperature and oven temperature constant
- Always have spare parts ready
- Record the normal back pressure so you can easily spot changes
Always display the pressure profile during your LC runs. Over time you will learn a lot about the condition of your system and you will be able to recognise the error based on the pressure.
In the next two course units, we will deal with a larger topic - changes in peak shapes.
Your Shimadzu LC team