Carryover/Ghost Peaks
GC Troubleshooting Course
7 - Carryover/Ghost Peaks
8 - Fronting Peaks
9 - Poor Peak Resolution
10 - Split Peaks
11 - Response Variability
12 - Retention Time Variability
13 - Course Summary & Test
Carryover/Ghost Peaks
The phenomenon of carryover (also known as ‘ghost peaks’) is where analytes fail to elute during one run, and so end up appearing in the following run, either as unexpected peaks, or as extra baseline noise. If you suspect that you have carryover, then run a blank after your sample to see exactly what peaks are being carried through.
Carryover is more to occur methods that require sample preparation (such as liquid injection, thermal desorption or SPME) than with gas injection methods. In these cases, the complex nature of the original sample matrix increases the possibility of slow-eluting or involatile components becoming ‘stuck’ in the system.
Comparison of Normal Chromatogram vs. Carryover Effect
Carryover is a phenomenon where unexpected peaks start appearing in sample chromatograms. In this example, the upper chromatogram shows
a sample run with 2 expected peaks at 3.75 minutes. The lower chromatogram shows a subsequent injection, where the compounds at 3.75 minutes
should not be present. The fact that these two peaks are still visible may indicate that these compounds are not being fully washed from the syringe
(increase solvent washes) or they are trapped in the inlet at higher concentrations (replace septum/liner).
Insufficient GC elution time
Insufficient GC elution time is the most obvious immediate cause of carryover, and the simplest one to resolve – simply try extending the GC run time by 5 minutes and ensure that the temperature at the end of the oven ramp is enough to ‘bake out’ everything that’s in the column.
Chromatogram overlaid with temperature ramp, showing how it brings off a high-boiling components (in red circle):
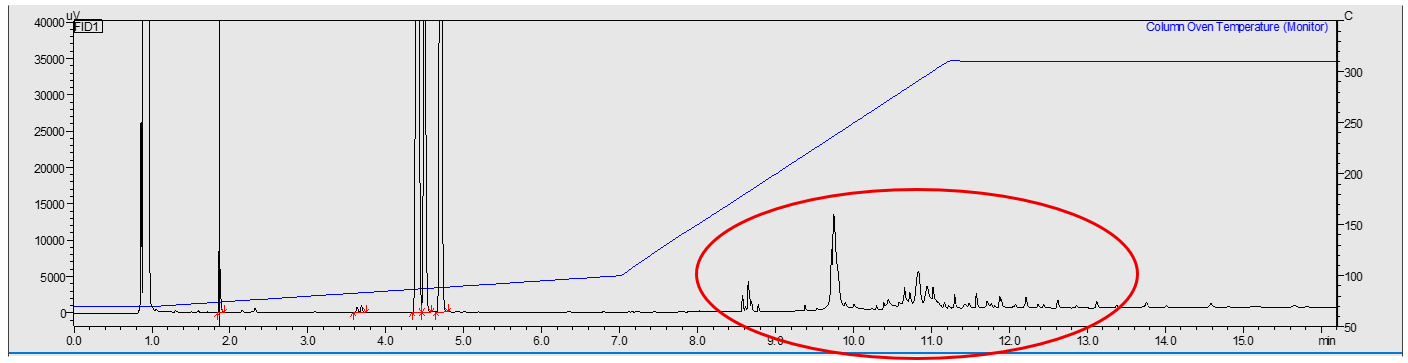
Extending the GC elution time and increasing the end-of-run temperature ramp is usually sufficient to resolve most cases of carryover.
Contamination
Carryover can also be caused by contamination in the syringe or rinse solvent, in this case either clean or replace the syringe and use a new batch of solvent.
Backflash
The other potential cause of carryover is backflash. This phenomenon is specific to liquid injections due to the majority of the sample injected being the extraction solvent. When this solvent hits the heated injector liner a vapour cloud is formed. If there is not enough space to contain it, then the excess vapour can flow into the gas supply line, taking the sample compounds with it. This excess sample can make its way back into the inlet contaminating subsequent analyses.
Online calculators are available that will check the expansion volume of your solvent.
If you think this could be the source of the problem, then solutions include:
- Injecting a smaller amount of solvent.
- Using a liner with a larger internal diameter.
- Increasing the head pressure (i.e. flowrate) to contain the vapour cloud.
- Using a slower injection rate.
- Lowering the inlet temperature.
- Using packing in the liner.
- Using pressure-pulse injection.
Related Resources